From internal pipelines, drains are transported by external ...
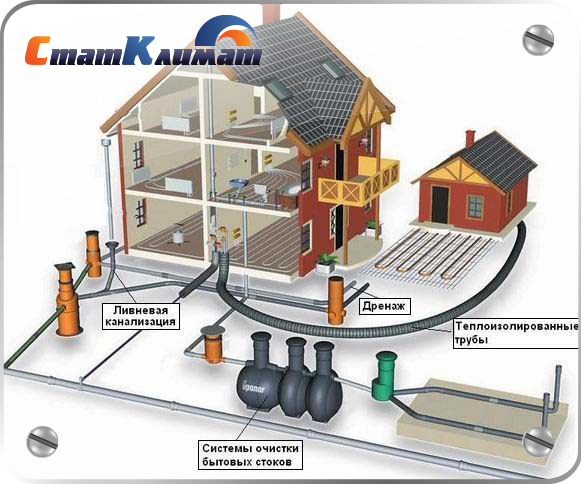
13.1. The surface of the storage area for materials, structures, products and equipment must be planned and compacted. With weak soils, the surface of the site can be compacted with crushed stone or laid with road slabs on a sandy foundation.
Warehousing of materials is carried out outside the prism of the collapse of the soil of loose recesses, and their placement within the prism of the collapse of the soil at the recesses with fastening is allowed subject to a preliminary verification of the stability of the fixed slope according to the passport of fastening or calculation taking into account the dynamic load.
Loads (except for ballast unloaded for track work) with a stack height of up to 1.2 m must be located at a distance of at least 2.0 m from the outer edge of the head of the crane track closest to the load of the rail, and at least 2.5 m at a higher height according to the requirements of GOST 12.3.009-76 *.
To drain surface water, a 1-2 ° slope should be made towards the external contour of the warehouse with the device, where necessary, ditches.
13.2. Slingers must know the places of storage of materials provided for in the PPRk.
13.3. The places of storage of materials and structures, as well as the places of installation of warehouse equipment are marked on construction site according to the example in figure 34.
1 - brick on pallets; 2 - spacer slabs - up to 2.5 m; 3 - span slabs - up to 2.5 m; 4 - extreme expansion plates - up to 2.5 m; 5 - stiffness walls - up to 2.5 m; 6 - crossbars - up to 2 m; 7 - flight of stairs - up to 2 m; 8 - wall panels in the pyramid - up to 2 m; 9 - stained glass in a pyramid; 10 - partitions in a pyramid with shelter from precipitation; 11 - columns - up to 2 m; 12 - platform for tilting structures.
Figure 34 - An approximate plan for the placement of goods at the on-site warehouse
Notes
1. Warehousing is carried out in such a way that the mass of structures corresponds to the crane capacity.
2. Temporary roads are arranged in such a way as to ensure acceptance of all goods within the crane's carrying capacity.
3. The scale (may not be shown in the PPRK) will facilitate the layout of goods within the cargo characteristics of the crane.
4. On the storage site, plates are installed with the name of the goods and their quantity in stacks.
13.4. Materials, structures, products and equipment should be placed in accordance with the requirements of standards, intersectoral rules for labor protection during loading and unloading and placement of goods, SNiP 12-03-2001 or technical specifications of manufacturers.
13.5. In the absence of standards and technical conditions of manufacturers, the following storage methods for the main types of materials and structures are recommended:
Brick in packages on pallets - no more than two tiers; in containers - in one tier, without containers - with a height of not more than 1.7 m. Brick should be stored in grades, and front - in colors and shades. In autumn and winter, it is recommended that brick stacks be covered with roofing sheets or roofing felt;
Wall panels - in pyramids or special cassettes in accordance with the passport for the specified equipment, taking into account the geometric dimensions of the products and their stability during storage;
Partition panels - vertically in special cassettes in accordance with the passport for the cassette. Gypsum concrete panels may be installed in a pyramid with a deviation from the vertical by an angle of not more than 10 °. Gypsum concrete partitions must be protected from precipitation;
Wall blocks - stacked in two tiers on lining and with gaskets;
Floor slabs - in a stack with a height of not more than 2.5 m on linings and with gaskets that are placed perpendicular to the voids or working span;
Crossbars and columns - in a stack up to 2 m high on linings and with laying;
Base blocks and basement wall blocks - in a stack of not more than 2.6 m high on linings and with gaskets;
Rigidity walls, depending on the type of transportation from the factory, in pyramids or similar to floor slabs;
Round wood - in a stack of a height of not more than 1.5 m with gaskets between the rows and the installation of stops against rolling; the width of the stack less than its height is not allowed;
Lumber - in a stack, the height of which during ordinary stacking is no more than half the width of the stack, and when laying in cages - no more than the width of the stack. In any case, the height of the stack should not exceed 3 m;
Fine metal - into a rack not exceeding 1.5 m high;
Sanitary and ventilation units - in a stack of a height of not more than 2.0 m on linings and with gaskets;
Oversized and heavy equipment and its parts - in one tier on lining;
Glass in drawers and rolled materials - vertically in a row on lining;
Bitumen - in a special container, excluding its spreading;
Ferrous rolled metals (sheet steel, channels, I-beams, section steel) - in a stack up to 1.5 m high on linings and with gaskets;
Heat-insulating materials - in a stack up to 1.2 m high, store in a closed, dry room;
Pipes with a diameter of up to 300 mm - in a stack up to 3 m high on linings and with gaskets with end stops;
Pipes with a diameter of more than 300 mm - in a stack up to 3 m high in the saddle without gaskets with end stops.
The bottom row of pipes should be laid on liners, reinforced with metal inventory shoes or end stops securely fixed to the lining.
When storing reinforced concrete elements having loops (plates, blocks, beams, etc.), the height of the gaskets should be no less than 20 mm greater than the protruding part of the mounting loops.
Warehousing of other materials, structures and products should be carried out in accordance with the requirements of standards and technical conditions for them.
13.6. Between stacks (racks) there must be provided passages with a width of at least 1 m and passages, the width of which depends on the dimensions of the vehicles and cranes serving the warehouse.
13.7. When storing goods, the factory marking should be visible from the aisles.
13.8. It is advisable to place panels of the same brands in the pyramids. The panels should fit snugly across the entire plane. Unilateral loading of pyramids is not allowed.
It is necessary to install products in cassettes, pyramids and other equipment of the on-site warehouse so that during storage they cannot lose stability, both the products themselves and the warehouse equipment. Products are installed taking into account their geometric dimensions and shapes.
13.9. There should be a distance of at least 200 mm between stacks of structures of the same name stacked side by side (floor slabs), or between structures in a stack (beams, columns).
10/13. The height of the stack or a number of stacks on a common gasket should not exceed one and a half width.
11/13. Gaskets are stacked vertically in stacks. The location of the gaskets depends on the operating conditions of the product in the structure.
12/13. Structures and products of one-dimensional length should be stored in each stack.
13.13. When arranging materials and structures, it is necessary to take into account the requirements of PPB 01-03.
Storage of materials and structures over underground utilities or in the security zone is allowed only with the written permission of their owner.
13.14. In case of changing conditions or in case of production need, the person responsible for the safe work of cranes can make additions and changes to the storage scheme of materials and structures provided for in the design documentation, in compliance with standards, technical conditions of manufacturers and other regulatory and technical documentation, approved by the State Supervision Authority and taking into account the cargo characteristics of the used cranes, access roads and parking lots; at the same time, the specified person is obliged to give the slingers a written scheme for storing goods in written form, the second copy of the scheme is attached to the PPRk.
When drawing up a storage scheme, special attention is paid to observing the dimensions of the aisles, dimensions and methods of storage, and the inadmissibility of overloading storage places.
13.15. In cramped conditions, in the absence of storage sites, it is allowed to store materials and structures on the floors (coatings) of existing and reconstructed buildings with the written permission of the author of the project and the development of necessary measures to ensure the stability of the building (structure).
Warehouses for the storage of inert materials must be arranged at the enterprises processing these materials, since the release of products from plants rarely quite corresponds to its quantity produced daily. The need for large warehouses also arises in cases where stone crushing plants operate year-round, and the finished product is transported only by water, that is, sometimes seasonally. Washing and sorting plants usually operate only in the warm season, since washing in the cold is impossible, and it is not economically feasible to arrange the heating of these plants. The size of inert factory warehouses is set when designing a plant, depending on the need to accumulate temporarily excess products under transport conditions, seasonality of work, delivery for construction, etc.
Warehouses of inert materials at factories are mostly open; bunkers are arranged only for more convenient loading of materials on vehicles.
1 - sorting compartment; 2 - bunkers; 3 - inclined belt conveyor; 4 - distribution belt conveyor; 5 - stacks of materials; 6 - collective conveyor belt; 7 - vacation department; 8 - collective conveyor belt in the sorting compartment; 9 - transfer belt conveyor; 10 - reversible belt conveyor; And - cantilever movable belt conveyor; 12 - loading crane with a grab; 13-rolling stock; 14-unloading trolley; 15 - expansion of the warehouse with a rope scraper; 16 - bucket rope scraper; 17- movable tower of the cable scraper
Open warehouses are very often linearly extended. For the formation of such linear warehouses a high overpass is arranged on wooden or iron poles supporting the trusses along which the conveyor belt or a group of conveyor belts feed material from the sorting compartment to the finished goods warehouse.
Both the supports of the flyover and the trusses are made of a very light design in accordance with the light load.
Each grade of material has its own stack; the stacks are separated by walls, or are located at such a distance from each other at which the lower parts do not touch them. Often there is a device with the separation of stacks of vertical transverse walls, which are sometimes used as the foundations of the support racks of the flyover. With wooden supports, you can sheathe their lower parts on both sides with boards or plates. Be sure to check the stability and strength of the walls for one-sided pressure of the material.
Only one sort of materials (or a certain mixture of them) can be transferred at any given moment with one conveyor belt going over the overpass, and therefore it is necessary to have bins in the sorting department, into which materials come from the screens and from which they are alternately unloaded onto the warehouse conveyor belt or another grade of material or a specific mixture of materials.
Material is discharged from the conveyor belt into piles by a mobile unloading trolley 14 . Instead of unloading with the help of this trolley, sometimes a movable reversible belt conveyor 10 is used (i.e., with the movement of the tape in one direction or another - II) Material is unloaded from one or the other end of this conveyor; this conveyor can also move along rails along the overpass so that its shipping end is located above the corresponding stack.
To increase the transverse dimensions of the stacks, it is possible to use mobile cantilever belt conveyors of the so-called "airplane" type ( III), which receives materials from the main conveyor belt through a mobile unloading trolley. In some cases, rope scrapers ( IV).
A tunnel (usually reinforced concrete) is arranged under the stacks for a collective conveyor belt, to which material from the stacks enters through openings in the tunnel ceiling equipped with gates.
1 - a cylindrical tower with sector offices adjacent to it; 2 - flat vibrating screens; 3 - belt conveyor feeding material for sorting; 4 - rope scraper with a movable tower; 5 - collective belt conveyor feeding material from the warehouse to the supply bins; 6 - sector warehouses of materials
It is rational to arrange warehouses for inert materials with a sector arrangement of stacks with different fractions. Sector warehouse allows you to place a lot of material in a limited area. In this system, the sorting department of the plant can be located at the top of the cylindrical tower. The lower part of the tower is buried in the ground. Radial walls adjoin the tower, dividing the warehouse into sectors and forming sector pockets near the tower itself, which are covered with grades of material coming into them directly from the screens through the gutters. Excess material exceeding the capacity of the pockets is stretched along the corresponding warehouse sector with a rope scraper, forming a spare stack. In the wall of the lower part of the tower against each sector there is an opening equipped with a shutter and a tray, through which material enters the lower end of the collective conveyor belt, which feeds the material to a concrete plant or loading bunkers. The shutters allow you to adjust the flow of material to the tape from each pocket, and therefore you can send from the warehouse not only any particular grade of inert material, but also a mixture of different grades in any proportion.
The scheme of unloading materials and feeding to a concrete plant using a rope scraper and a conveyor belt. 1 - railway; 2 - trench for the material; 3 - conveyor belt to a concrete plant; 4 - bucket rope scraper; 5 - reloading funnel; 6 - inclined plane; 7- mast and winch
As material is consumed from the pocket, the latter is replenished from the spare stack with a rope scraper. The winch of the cable scraper, together with the tower for blocks, is mounted on a trolley moving along a circular rail track. In small installations, the winch is mounted on a truck or a tractor trailer. Blocks for the return rope move along a circular channel, fortified at the top of the tower at the floor level of the sorting compartment.
The materials are dispensed from warehouses to vehicles through dispensing bins. When loading onto rail or road transport, transport units are fed under a bunker containing a particular fraction or a finished mixture of products. For loading on water transport, bunkers are arranged along the loading line and the contents of the bunkers are dumped directly into the barge. Usually, in this case, sand is separately loaded and gravel or gravel separately. Scheme of material movement using cable-stayed derrick from unloading rail trenches to stacks and to a concrete plant:
1 - cement warehouse; 2 - concrete plant; 3 - unloading trenches; 4 - winch; 6 - sand; 6 - fine gravel - large gravel; 8 - winch
Such a scheme is often used. The material is unloaded from the trains into a trench located along the track. A rope scraper bucket moves along the trench, which pulls the material and puts it through a funnel onto the conveyor belt, which transfers the material to the concrete plant. Sometimes the material is fed by a cable scraper directly to the concrete plant. From railroad trenches, materials can also be reloaded with the help of a cable-stayed derrick into spare stacks or directly into the bunkers of a concrete plant. Sometimes trains or trucks transporting material to a building are transported to an overpass and dumped from them into high stacks under which conveyor belts pass.
The figure shows the device used in one of the sections of the construction of the Moscow-Volga Canal.
If inert materials are delivered by water, then their unloading can be performed by mobile cranes with a clamshell bucket or stationary derricks. Material is loaded into an intermediate hopper, under which a conveyor belt passes, moving the material to warehouses at a concrete plant, or directly into the hopper of a concrete plant.
When delivering materials to separately located concrete mixers, stacks are located as close as possible to them.
On-site warehouse. The materials and structures ordered for construction are delivered to on-site warehouses and placed on them in accordance with the project of work and on-site warehouse schemes shown on the construction plan.
For each material, a place is assigned that is determined so that the transportation of material to the workplace takes as little labor and time as possible. Places for receiving and overloading the solution are also placed.
Storage areas of materials (by type) are separated from each other through openings at least 1 m wide. In each zone, materials and products are stacked by brand. Stacks of materials are placed at 0.7 m intervals so that it is convenient to approach and sling a load (material). With a large number of similar products at the places of storage, they are set with indicators of series and brands of products.
Reinforced concrete and concrete parts and blocks are positioned so that their factory markings can be read from the side of the aisle or driveway, and the mounting loops of the products stacked in stacks are turned up.
Prefabricated parts are stacked so that it is convenient to sling them during loading; the height of stacks should not exceed for precast concrete products - 2 ... 2.5 m.
Products are placed so that they do not deform, do not become dirty, and their front surfaces (textures) do not deteriorate. Laying structures and parts is allowed only on rectangular linings and gaskets; water should not stagnate on structures, for which they need to be laid with a slight slope.
Through holes in concrete products are closed so that snow does not get there and ice does not form. Reinforced concrete parts are periodically cleaned of snow and ice.
Passports and certificates for products and materials. Supplying factories supply the materials and products supplied to the construction site with a passport or certificate. The passport is evidence that the products are made in accordance with the project (working drawings), applicable state standards or technical specifications. Acceptance of prefabricated structures without passports is prohibited.
The passport shall indicate the name of the products in accordance with GOST or technical specifications and their symbol (index), the number of GOST or technical specifications, the number of products in the batch, the date of manufacture and acceptance of the batch by the technical control department (QC) and the number of the QC inspector, concrete grade, tempering strength concrete (as a percentage of design) at the time of acceptance.
For each batch of the same type of prefabricated reinforced concrete structures, the manufacturer submits to the construction organization test certificates for control concrete samples.
Each prefabricated reinforced concrete and concrete product must have a visible marking made with indelible paint, which indicates the brand of the manufacturer, the passport number of the product, index, and the number of the quality control department of the company. On products whose top is difficult to distinguish from the bottom (slabs, beams), the inscription “Top” is made or the letter B is written in the upper part and N. is written in the lower part. Stamps on such products are placed so that the base of the mark faces the lower surface products, which allows to judge about his working position. If there are no loops on the elements, the sling places are marked in accordance with the design.
Acceptance of structures and products. When accepting structures arriving for installation, their quality is checked by external inspection. Make sure that the product has no deformations or other damage (spalls), its front surface (textured layer) complies with the design requirements. Selectively control the compliance of the geometric dimensions of the elements with the design data, the correct location of embedded parts, outlets, grooves, niches, holes, fixing devices, quarters, the safety of mounted parts of sanitary, electrical and other equipment.
Elements of prefabricated structures that have deviations exceeding the tolerance, or other serious defects, are rejected, which constitutes the act.
Warehousing of materials. Warehousing rules are indicated in technological maps and labor process maps.
Bricks are placed according to grades, and front bricks - also by the color of the front surface. If the brick is delivered to the construction site without containers or packages, then it is unloaded manually, stacked in piles up to 1.6 m high or on pallets. At the same time, brick with empty voids is laid down with voids so that water does not penetrate into them, which, when frozen, can destroy the brick. Front bricks are stacked in regular rows. The height of the stack should not exceed 1.5 m. Packages with bricks are installed in on-site storage in stacks, in one or two tiers.
Ceramic wall and facing stones, as well as stones from other materials, unload, store, as well as front brick. Claddings made of ceramic, concrete and other slabs are stored in containers or stacks on wooden gaskets, laid in 2 ... 3 rows on a rib facing each other.
Prefabricated parts and structures are installed on wooden inventory pads and gaskets, placing them in places provided by the working drawings and marked on the elements.
Platforms for stacks in warehouses are pre-leveled, the soil is compacted to prevent subsidence from sagging. Otherwise, the product will not rely on linings, but on the ground and will break due to improper load distribution.
Gaskets between products stacked in a stack are placed one above the other, strictly vertically. The thickness of the gaskets is selected so that the overlying elements do not rest on the hinges or protruding parts of the underlying elements. Linings for stacks of products usually have a cross section of at least 100 X 100 mm.
Prefabricated concrete and reinforced concrete elements are stacked according to the following schemes.
The blocks of foundations (Fig. 107, a) and basement walls are stacked with heights of not more than 2.25 m on linings and gaskets, which are installed at a distance of 30 ... 50 cm from the ends of the blocks.
Fig. 107. Stacks of reinforced concrete structures: a - foundation beams, b - crossbars, c - floor slabs, d - staircases
Rectangular crossbars (runs) up to 600 mm high (Fig. 107, b) are stacked on a rib no more than three rows in height, with linings and gaskets located at distances of 0.5 ... 1 m from the ends; the bolts of the upper row in stacks are fastened together for mounting loops.
Multi-hollow floor slabs (Fig. 107, c) and floor slabs are stacked in stacks with a height of not more than 2.5 m flat up to 8 ... 10 rows, depending on the strength of the warehouse base; gaskets and linings are perpendicular to the voids at a distance of 25 ... 40 cm from the edges of the plate. When stacking products in stacks, it is necessary to monitor the correct placement of gaskets and products themselves - improper storage of precast concrete elements (Fig. 108, a, b) inevitably leads to their destruction.
Fig. 108. Destruction reinforced concrete slabs with improper storage: a - the pads are not located on one vertical, 6 - three gaskets instead of two and not one vertical
Stairs (Fig. 107, d) are stored steps up; the height of the stacks is 5 ... 6 rows. Lining and gaskets are placed along the marches at a distance of 15 ... 20 cm from their edges. Stairs are placed in a horizontal position with a height of not more than four rows, linings and gaskets are installed at a distance of 15 ... 20 cm from the ends.
Fig. 109. Warehousing of wall panels and blocks: a - panels, 6 - outdoor external blocks, c - horizontal blocks; 1 - pyramid frame, 2 - stepladder and fencing, 3 - wall panels (partitions), 4 - supporting part
It is recommended to store large-panel partitions, wall panels (Fig. 109, a) and solid flat floor overlapping panels the size of a room in a vertical or slightly inclined position in cassettes or pyramids. The supporting parts 4 of the pyramids have a slight slope towards the pyramid 1, due to which a right angle is formed between the pyramid and the support. Due to this, the panels 3 installed in the pyramid are supported on the flooring of the pyramid supports with the entire face area, and not with the edge, which eliminates damage to the panel faces. ,
Large concrete blocks of the external (Fig. 109, b) and internal walls with a height of more than 1 m are placed in a row vertically in the design position on the lining of the boards with the mounting loops up; when two blocks of external walls are installed side by side, they have a textured layer outward (indicated by a dotted line).
Horizontal wall blocks (Fig. 109, c) up to 800 mm high are laid in several tiers on linings with a distance of at least 50 mm from the block faces (to avoid damage to the textured layer and the formation of frost) and not more than 1/5 of the length of the element. The total height of the stack should not exceed 2.5 m.
Fig. 110. Storage of building frame structures: a - columns, beams, c - reinforced concrete beams, d - wall panels
Columns (Fig. 110, a) are stored in stock in stacks of 3 ... 4 rows on gaskets, usually at a distance of 1/5 ... 1/6 of the length of the column from the ends. Reinforced concrete crossbars are also stacked in piles (Fig. 110, b).
Farms and beams (Fig. 110, c) with a height of more than 600 mm are stored in a vertical or slightly inclined position with the device of vertical stops that ensure the stability of structures, and with the installation of vertical gaskets between them.
Steel structures are recommended to be laid in the following ways: beams, girders, half-timbered elements (rolling and composite) with the vertical position of the walls - in stacks with a cross-arrangement of rows of beams in a stack on two linings; trusses and beams with a height of more than 0.6 m - in a vertical or slightly inclined position with the device of vertical stops, which ensure the stability of structures and with the installation of vertical gaskets between separate structures. In the same position they store lantern farms, window ceilings, stairs and other structures.