From internal pipelines, drains are transported by external ...
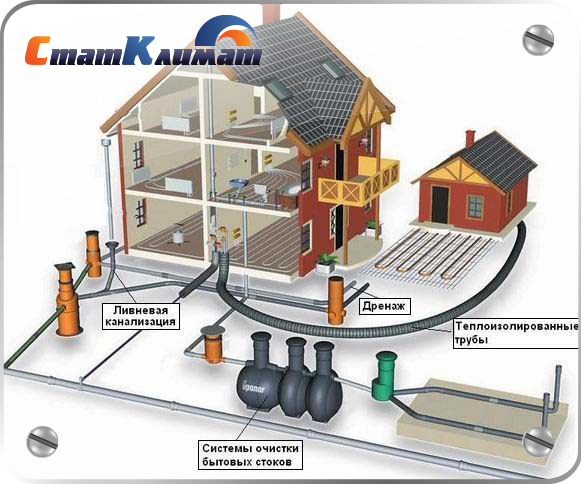
For centuries, marble has been used for the interior and exterior of any building, but not everyone uses such material, since it is expensive, and deposits are located in the mountains, where it is difficult to deliver the necessary equipment for its extraction. And due to the fact that its processing increases production costs in such a way, and production is associated with the destruction of already limited deposits, people tried to produce this material. Today, concrete marble is widely used not only for exterior decoration, but it is surrounded by fountains, flower girls, columns, vases, pavements are made, and it is also suitable for landscape design.
The method of manufacturing such a material from a simple concrete mixture allows us to create high-quality and durable artificial stone, which has a glossy surface, from Portland cement and dry sand. Tiles are made using this technology, using a frost-resistant mixture with low water absorption. For this technique, special forms imitating the surface of stone paving stones are used.
The service life is quite long, since the strength of artificial marble slabs is compared with products from wild stone and granite pavers. The assembly of such material is simple, since the form has precise shapes and grooves, which make it possible to tightly stack and join the tiles.
Consider how to do it yourself, at home. In order to make it is necessary to have the following materials:
In order to understand what constitutes technology for the manufacture of marble tiles from concrete, consider a special guide that professionals offer:
Before you make marble from concrete, calculate the right amount of water, which is dependent on the proportion of cement included in the composition.
First, determine the value of the coefficient, which indicates the necessary for hydration (the process in which the grains of the composition are enveloped in water) the amount of liquid for the cement mortar.
This value is expressed by the formula:
Coefficient \u003d Water / Cement
In order for the mixture to be closed, use the following indicators:
But this takes into account that the sand should be dry.
Consider a specific example.
Water / cement \u003d 0.25
From this it is concluded that in order to determine the required amount of liquid it is necessary:
Cement X 0.25 \u003d Water;
Therefore, the amount of water is:
15 X 0.25 \u003d 3.75 kg, i.e. 3.75 liters.
Among the advantages of this material, the fact that it can be manufactured independently without special work skills, that is, its availability for a wide range of consumers, stands out.
Compared to natural marble, the artificial material is lightweight, which makes it possible to clad even inclined surfaces. This material does not need to be further processed. The shape and thickness of the tiles are set initially, they depend on the needs of the owner. Applying this material for cladding, you can achieve a embossed surface, but its smoothness will not be affected. For example, the front side can be made like wood, sea ripples, bricks, etc.
Tiles are connected as puzzles, which gives reliable adhesion not only between the individual elements, but also within the same layer.
Self-made marble can have a different color, and seven coloring methods:
With the use of such finishes, the interior of the house acquires originality and sophistication, and the production of marble from concrete has entered the world stage as the most cost-effective business. But it is worth noting that it is very easy to make the product you need on your own, without putting much effort and without making big financial investments.
Recently, the technology of manufacturing concrete products with colored stains that imitate marble has gained great popularity. There is a logical explanation for this, because marble is able to give prestige and sophistication to the facades of buildings or to decorate the premises from the inside. In addition, the advantages of this technology include the fact that marble can be made of concrete at home.
The technology for the production of artificial marble from concrete is quite simple, so every home craftsman can make such a material. However, some knowledge is still necessary.
If the work is done correctly, the material will turn out to be so similar to marble that an ordinary passer-by is unlikely to guess that, for example, an artificial stone was used for the fence.
In addition, this material has several advantages:
Before we begin to make stone, we should prepare a certain set of materials:
In addition, you will need more forms in which the solution will be poured. For these purposes, it is best to use special polymer forms. If you can’t find them, you can use any other forms made of plastic.
For example, if you want to make window sills from concrete marbled, then you should look for suitable plastic trays. In extreme cases, you can execute the forms yourself by fastening plastic panels together.
It is also desirable to have a vibration table, which can be done with your own hands. If you will be engaged in the production of marble once, then you can do without it by shaking the mixture manually. Vibration will allow the solution to condense and eventually make a denser material.
I must say that the same technology can produce polymer concrete.
The only thing, instead of cement in this case, thermosetting resins are used as a binder:
Note!
In the manufacture of polymer concrete, a larger amount of filler is added to the composition than in ordinary concrete mortar.
After all the materials have been prepared, you can begin to work. The manufacture of artificial marble and polymer concrete begins with the preparation of the mortar.
Concrete mortar is mixed in a standard proportion - 1: 3. At the same time, calcium carbonate or other neutral fillers similar to it is best used as a filler.
If polymer concrete is kneaded, then a solution in the ratio of 1: 4 should be performed. Coarse fillers are used as filler.
In particular, crushed in the form of gravel or coarse sand are suitable for these purposes:
Further instructions are as follows:
Here, perhaps, is the entire composition of the production of artificial marble from concrete. I must say that there are other technologies for the manufacture of artificial stone. Moreover, some of them are even simpler and do not require finishing polishing.
However, at home, the above method is the most affordable.
Note!
Since the resulting material will be sufficiently strong, it can only be processed with a diamond tool, in particular, in addition to the above grinding, an effective method is cutting reinforced concrete with diamond wheels, as well as diamond drilling holes in concrete.
On the picture - faux marble In bathroom
Most often, artificial marble is used to decorate fences outside. However, such material can be a great alternative. ceramic tile, for example, in the bathroom. In addition, "concrete marble" can be used as countertops in the kitchen.
It can also be an excellent decoration for fireplaces, which are not only the center of home comfort, but also a sign of luxury. If the interior of the room is made in a classic style, then the material can be used as a floor covering.
In any case, wherever you use marble, its use will be a sign of good taste and luxury!
From the video in this article, you can get more information on making artificial marble at home.
Modern analogues of traditional natural materials have received the widest distribution today. The advantages of using artificial stone in the interior design are innumerable, just mention the exceptional strength of the material and the relatively low cost.
The possibility of self-manufacturing, ease of installation and processing of the finished product, as well as the use of innovative technologies in the manufacture - all these aspects are described in detail in the information in this article.
The use of natural stone in the design of residential and public buildings has more than one hundred years of positive use. Such cladding has always been the prerogative of the upper strata of society, but with the advent of artificial analogues, such luxury has become more affordable.
You can find out how it looks from this article.
This significantly expands the scope of use and contributes to the popularization of products made of artificial marble.
Advantages of using artificial stone in the interior:
You can find out what it is from this article.
On the video - artificial marble manufacturing technology:
At the same time, one should not forget about some of the features of this material: the finished product must be properly certified, and if it is self-made, it will be useful to study the production technology in advance, stock up with all the necessary materials and tools. The manufacture of artificial marble requires compliance with safety rules, since during work there is contact with chemicals.
Here everything is limited only by your imagination! Artificial marble is widely used as a facing material, both indoors and outdoors. Facades made of artificial marble are characterized by absolute resistance to atmospheric phenomena, ultraviolet radiation and mechanical damage. The scope of this material is very wide, good strength and harmlessness to others will allow the material to perform the most diverse tasks.
On the video - the use of artificial marble:
A few examples of the use of artificial stone:
In principle, artificial stone in general and marble in particular can be used to decorate any interior detail. Depending on the type of molding sand, marble can form a rather thin layer, which is successfully used for internal wall covering instead of traditional wallpaper.
In order to better understand the possibility and technology of self-production of artificial marble, it is necessary to study in more detail the qualitative composition of the molding mixture and the types of this material. A brief overview and a master class on making marble with your own hands - further in our article.
The following types of artificial marble are distinguished:
You should familiarize yourself with the undisputed leader of this list - cast artificial marble, which is most in demand in terms of performance and ease of manufacture.
Casting marble contains polyester resins, mineral fillers, water and special pigments. Thanks to its natural components, marble is obtained as natural as possible and has excellent characteristics. Thanks to dyes, you can recreate the structure of almost any natural stone, but imitation of marble has gained the most popularity.
The algorithm for creating cast marble products:
The resulting part is then subjected to grinding for the final removal of burrs and impregnations of the mixture. Also, the surface is polished with a special brush to give smoothness and visual appeal to the product.
The process of making artificial marble with our own hands is not much different from the industrial method. The tool can be used the same, only expensive forms to create a single product will be impractical to buy. That is why there are many ways to make matrices yourself.
Typically, plastic containers of suitable size and configuration are used for this. For the manufacture of a conventional plate, a wooden pallet with reclining sides will be enough. Dimensional accuracy will not be so important, because the finished product can be cut to the required values.
The presence of a vibrating table will greatly facilitate the task and make the structure of the artificial stone more durable and uniform, but for lack of a better one can use the manual method of mixing. The gelcoat layer can also be applied with a hand gun or a regular paint brush. In general, any home master can independently choose what to replace industrial equipment with. Special mixing containers can be successfully replaced with a “mixer” nozzle for an electric drill. The top layer of the home-made form is insulated with a plastic film for successful removal from the hardened mass.
Artificial marble is an excellent finishing material, which has found the widest distribution in everyday use. It is used for aesthetically attractive and durable cladding of internal walls and external facades of buildings.
In the video -
Floor tiles made of this material are extremely resistant to abrasion and mechanical damage, and kitchen worktops and aprons very successfully resist aggressive effects temperature condition and chemicals.
Sinks made of artificial marble are distinguished by their superior design and trouble-free operation. Do it yourself artificial marble will significantly reduce the cost and will allow you to get original configurations and colors of finished products.
but it is a beautiful, and most importantly inexpensive finishing material. The simplicity of its production makes it possible to make artificial marble with your own hands. It can be used both for interior decoration premises, and for outdoor decoration in landscape design.
To begin with, let's figure out what decorative concrete is and consider its composition. The basis for artificial marble is a cement-sand mixture with various additives and color. Marble made of concrete is durable, fireproof, and is characterized by environmentally friendly components in production. Found the main application in the production of the following elements of construction:
There is nothing complicated in the technology for the production of decorative marble, but some equipment is needed:
To prepare a solution of artificial marble, we need:
A bit about color
If you want to achieve saturated shades, it is better to use white cement. This will not only make the product brighter, but also stronger, since the amount of dye for such marble will need less. Dyes can be of different types:
All other components are added according to the data on the packaging and mixed for 10 minutes.
The finished solution should have a consistency of thick sour cream. After mixing, put the finished mixture into molds and put them on a vibrating table. A little “shake” to fill all the corners and bends and put aside for a day in a room protected from direct sunlight. After exposure, we can pull out the finished product from the mold.
Pros:
Minuses:
This concludes the review article on the manufacture of marble from concrete a, in further articles we will delve deeper into the production of artificial marble. You can leave your questions in the comments.
|
Marble, which has excellent aesthetic qualities, has always been a valuable material, but because of its high cost, it is rarely bought. Therefore, artificial marble was invented, which is not inferior in its characteristics to natural.
The current situation in the field of building materials, especially made of artificial stone, can be described as accompanied by growing demand. At the same time, beginning and experienced businessmen who want to engage in this production should not only satisfy such demand, but also stimulate it.
Artificial marble is a material that is made on the basis of acrylic resin and filler, imitating the properties and appearance of natural stone. It is environmentally friendly and wear-resistant, easy to operate and maintain. The substance is characterized by high strength, reliability, excellent aesthetic characteristics and most importantly - it is cheaper than natural. Various textures and colors make this material unique and popular in the construction market.
The scope of its application is wide, it is used for external surfaces (countertops, tables, window sills, bar counters), during construction, restoration of premises and in industry.
The manufacturing process as a whole is simple. It consists in mixing the ingredients and placing them in a mold until hardened. Depending on the components, marble is divided into types:
He is one of the most popular species. It is a composite material made of mineral filler (quartz, marble chips), cured polyester resin and pigments, dyes.
Manufacturing technology lmarble:
The technology of manufacturing marble from concrete:
The technology for the production of artificial marble from concrete makes it possible to obtain a durable material that looks practically the same as natural stone. For its manufacture it is necessary:
The resulting products have a streamlined glossy surface. After removal from the form, further processing is not necessary. Tiles using this technology are made from frost-resistant concrete in various author's forms, which imitates old paving stones or paving glossy surfaces. Such material is durable and reliable, does not lend itself to mechanical damage.
This type of marble is one of the newest. decoration materials. It consists of acrylic polymers and marble chips. The result is liquid marble - a flexible, flexible, durable and lightweight material. It can be easily cut, covering them with different surfaces. It gives you the opportunity to align the curved walls, hide oversights and flaws. This material is faced with columns, arches, stairs.
The amount to organize this business depends on many factors - the scale of the project, assortment, and manufacturing technology. Consider a rough financial business plan for faux marble.
Starting costs:
The production of cast and flexible marble requires the following monthly costs:
The price depends on the thickness of the product, type and final product to be manufactured. For example, to buy a window sill made of cast marble costs 8800 rubles per square meter.
On average, the gross revenue of this type of enterprise will amount to 500 thousand rubles. (minimum threshold taken). In this case, the net income will be 120 thousand rubles. (500-160-120-40-60).
Given these production indicators, the payback period will be 2 months.
For the production and sale of products, you must register as an individual entrepreneur or LLC. Registering an IP is simple, with a minimum package of documents required. The procedure for opening an LLC is more time-consuming, but it opens up great opportunities and eliminates financial risk (since the founder of the company is responsible for the business only with the authorized capital, while the sole proprietor is responsible for the personal property). The choice of legal form depends on the volume of production, source of financing, distribution channels.
To sell products you will need:
This business idea does not require the purchase of high-tech equipment. Since the manufacturing technology is simple, it is necessary to buy the following equipment for the production of artificial marble: