From internal pipelines, drains are transported by external ...
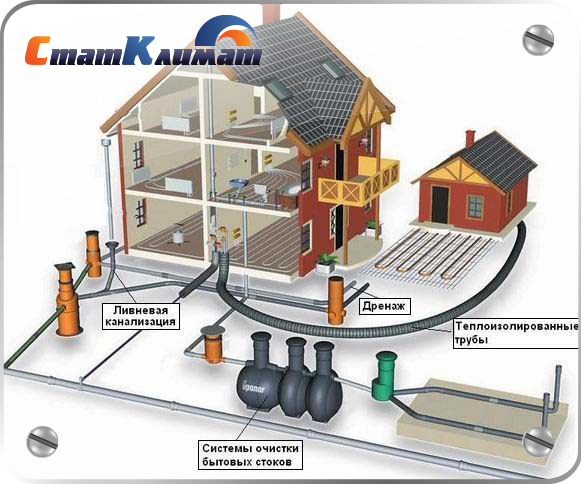
Double-glazed windows made of prefabricated glass panels are beautiful and comfortable. But they have one drawback: if the glass is accidentally broken, then often it is necessary to replace the whole window, and this is a long, and expensive. Therefore, if you need windows for a summer house or for some kind of outbuilding, plastic windows economically disadvantageous. It is much easier and cheaper to install wood. And making wooden windows with your own hands is not so difficult, although it would be unfair to call this work simple.
Wooden windows are able to maintain the necessary level of humidity in the house, which favorably affects the indoor microclimate of the room.
Making a window in a home workshop, and in addition without having sufficient qualifications, it is impossible to achieve its complete tightness and reliable sound insulation. Therefore, for a residential building, it is better to order windows for professionals. But for the veranda, bathhouse, barn or garage, anyone can try to make wooden windows with their own hands, if only the right materials and tools are at hand.
When deciding to make a window yourself, you need to responsibly approach the choice of material. The tree must be well dried, otherwise in the future we can not avoid warping and shrinkage of raw wood. Also, the board should not have chips, cracks, knots, etc.
The window construction itself consists of a box that is inserted into the window opening and fixed rigidly in it, and the frame itself with glass inserted. For a box, it is better to take a wooden board with a cross section of 150x50 mm, and for a frame usually use a wooden bar with a cross section of 60x40 mm.
For windows use pine or oak boards. Oak is much more durable than pine, but also much more difficult to process. Therefore, novice joiners first make window structures from pine and, only having gained experience and “having gotten a hand”, go to work with oak.
Of the tools for assembling the window you will need:
Back to the table of contents
Despite the simplicity of manufacture, the box must be treated with great respect. After all, it is the box fixed in the window opening that will take on the main load. If it cracks or bends under the weight of the wall, it will be impossible to insert a window into it, and the glass will be burst at the inserted one.
Begin manufacturing boxes with blanks. To do this, 2 pieces are cut off from the board, the length corresponding to the width of the window opening, and 2 pieces corresponding to its length. The ends of the boards corresponding to the width of the box, using a jigsaw and a chisel, turn into a spike 20 cm thick. And in the ends of the boards, measured in length, the same thickness of the groove is made.
After that, at each board you need to choose a groove for a width of 50 mm and a depth of 3-4 mm. The resulting ridges will subsequently serve as a support for the window frame and contribute to better window tightness. Having finished sampling, all four sides of the box are interconnected.
The corners are fixed first with wood glue, and then two holes of Ø12-15 mm are made at the ends of the boards so that the drill passes through the top board and goes deeper into the bottom end by 10 mm. Then, wooden rods of the corresponding diameter are inserted into each hole. These rods provide fixed fixation of boards connected at right angles.
Typically, window frames are inserted into the wall directly during the construction of the walls, and frames after the end of the roof. Insert the box must be the selected side out. Since the ducts are subject to considerable loads for a rather long time, especially on their upper part, temporary struts are inserted in them to prevent warping.
These spacers are vertically inserted 25-30 mm boards, 10 mm longer than the distance between the transverse boards of the box. The lower part of the boards is cut evenly, and the upper one at a small (4-5º) angle, so that the spacer can be inserted more tightly inside the box, and subsequently it is easy to remove it from there. The number of spacers depends on the span and is taken at the rate of 1 spacer per 40-50 cm of width.
Back to the table of contents
The profile shape of the window frame depends on the number of inserted glasses and their thickness. With a single-glass profile, the frame has 2 grooves: 1 - for glass, 2 - for a more airtight insert into the box. For the double-glazed profile, you will need another additional groove. If you need three windows in the window, it is better to make an additional single-glass frame, which will be inserted into the box from the inside.
First you need to correctly saw the beam. Having measured the distance between the boards of the box, note the same on the beam, and then saw off, but not directly, but at an angle strictly of 45 °. Saw off the ends along a convergent path, i.e. one face remains the same length, and the opposite is shorter. If the window is planned to be hinged, then you need to saw off 4 box heights and 4 workpieces corresponding to half its width plus 3 cm.If everything is measured and sawn correctly, then the workpieces connected together should form a rectangle 1-2 mm smaller than the box’s inner perimeter.
On each blank, which will be attached to the window box, on one side of the long face with a planer, a selection of 10 mm wide and 5 mm deep is made to provide greater tightness when installing the frame in the box. On a short edge, the same sample sizes are also made. If the profile is single-glass, then one sample is made on the short edge at the diametrically opposite end of that made on the long edge. With a two-glass profile, samples are made from both ends of the short face.
On the remaining two bars, grooves are also made, but differently. They are made half the width and half the depth of the beam, but in mirror image. That is, they make grooves so that when they are in contact, the two halves are connected into a single structure. The same grooves must be provided for in the ends of the horizontal bars connected to the vertical bars (this is where the extra 3 cm of width will go).
Two semi-frames are assembled from these blanks. Further, as in the assembly of the box, holes are made at the ends, only smaller, Ø 8-10 mm. Then the ends are folded together and connected by wooden rods. For greater reliability, long self-tapping screws are screwed into the places of the end connections, be sure to drown their caps, and even better - the ends are fastened with metal corners.
Two assembled half frames are attached to the window frame using small cylindrical hinges, 2 for each half frame. The hinges are attached with screws: one half to the frame, the second to the window frame. In the static position, two half-frames are fixed with latches or latches.
If the window does not open, then two options for the window frame are possible. If the window itself is small, then 2 heights of the box and 2 of its width are sawn off for the frame. Further assembly operations of the frame are completely identical to the hinged window.
However, if the window is large, it is best to consider splitting the glass into two or three parts. The frame body itself is assembled in the same way, but 1 or 2 additional vertical beams are additionally mounted on it, on which grooves for glasses are made.
To do this, on the frame body in the middle or at a distance of 1/3 from the edges on the back of the frame, grooves are made to half the bar, and in width - to the width of the bar. On the additional blanks from the outside, the spikes of the same width and thickness are made. Then the spikes are inserted into the grooves and fastened with wood glue and self-tapping screws. Such frames are not attached, but simply inserted into the box. Their fixation is carried out in platbands, and the remaining slots are closed with mounting foam.
Instruction manual
Take a well-dried planed board, it will avoid window warping or shrinkage. Make a box for a wooden window. For its manufacture, you can use boards with a section of 50x150 mm. On the board, make a groove so that in profile the board has an L-shaped shape. The resulting comb will contribute to the tightness of the window. Use an electric planer for this work.
Then, in accordance with the size of the window opening, cut the board into 4 parts and connect them together. It is best to make such a connection with a straight spike and a straight groove. To create such a connection, you need to cut the spike on one board (which will have a horizontal position), and on the other a groove. This work can be done using a saw, hammer and chisel, or use a hand mill. Then, glue the joints with joinery glue and assemble the box. When assembling, it is important to ensure that the parts are joined at a 90 degree angle. To ensure a hard connection, drill a hole in the end and insert a wooden pin greased with glue into it. At the corners to the ends, install window metal corners to strengthen the box. After the glue dries, the box is ready.
Now you need to make a window frame, for which a beam with a section of 50x50 mm is used. The sequence of its manufacture is the same as the boxes. Make a profile using a hand milling cutter or an electric planer. To frame easily open and close, you need a gap between the frame and the box in 1-2 mm.
Related videos
note
Do-it-yourself wooden windows can be used on porches, balconies, in a bathhouse i.e. where the wooden window will serve as a fence from the environment. Consider making a single-door wooden window with your own hands. Now consider the design of a wooden window. The window consists of a box that is mounted in the window opening and the frame itself with glass. The box can be made of boards, for example, a cross section of 50x150mm.
Useful advice
Therefore, without special equipment, it is unlikely that it will be possible to make a frame of wood, like the one that is sold in stores. But for rooms in which there are no special requirements for windows, it is quite possible to make frames with your own hands. Consider how to make a window frame with your own hands, in a home workshop. To begin with, we will focus on the manufacture of a simple, single-leaf design. Everyone knows that wooden frames dry out over time, losing their shape.
Sources:
A bit of background. The windows in our house in Peterhof were rare: the year of manufacture was nine hundred and fifty with a tail, the fittings were Soviet-style latches, the exterior was the same as the “thirty-four” after the Kursk Bulge, thermal conductivity was excellent. In short, it was cold in winter, and the appearance, to put it mildly, did not satisfy even such an unnatural comrade as myself. The simplest one was to order plastic, but I really wanted to try my hand at carpentry, which resulted in a month of leisurely work in my free time.
Glued sash.
And here is the sash in the frame and also such a chipper so that water does not accumulate in the gap.
An almost finished product coated with Pinotex. In the back part there is still no double-glazed window.
I ordered double-glazed windows with two chambers with different glass thicknesses and different distances. If not mistaken, the formula was 4-10-6-12-4. Two windows (2 double-glazed windows in the back part, 2 - in the sash) took something about 9 thousand rubles. Bigger double-glazed windows (those that were installed in the deaf parts) were very heavy. The two nearly burst, while they pushed the frame with glass into the opening.
A new window in the opening. Well, since such a booze started, then I sawed, polished, and put new window sills.
Here already made slopes. Shtapik put it in about a month.
I must say right away that counting all these quarters, the grooves and spikes was tiring, and the final fine-tuning and grinding is a rather dreary task. However, in the year 15, the wife said the party “must” and puzzled the windows for the house in the village in the Novgorod province. The situation at that historical moment was such that ... Well, in general, there was no situation. I just bought a car, frantically nodding banknotes to fill up a hole in the budget, and then here you are - we would have four windows, but two of them open. Buying plastic is not reasonable, so I had to start the jointer, surface gage and other machinery again. This time it took less than a week, since the windows were much smaller, and I did not do double quarters in the wings, I managed one. Source material: bar 50 * 100. Process illustration:
Pair bonding. For lack of wime cost clamps.
The spikes and grooves are cut, the workpieces are assembled.
Make a rounded edge on the inside.
Here is such a joint.
We drill holes for fittings, with a milling cutter, we select the recesses for the metal platforms of the fittings.
Suspended for subsequent chemical processing. Jars of Pinotex under the table.
First layer: Pinotex Base. In the background are windows installed two years ago.
Second and third layers: white Pinotex Ultra.
The double-glazed window is single-chamber, since in winter no one lives in the village.
Apply carefully transparent sealant.
Suckers here at once were useful, otherwise everyone was lying around idle.
Window assembly with glazing bead and false binding.
My view from the rear.
Facade with new windows.
These are the pies with kittens.
Tool List: planer, planer, face saw, saw machine, milling cutter, belt and vibration grinders, chisels, mallet, screwdriver (drill), clamps, vernier caliper, square.
List of moral and psychological qualities: patience, accuracy, the ability not to break the tool, when it turns out that on the already processed and glued workpiece, the cut was done on the wrong side.
Guys, there’s nothing super complicated. The most difficult thing for me was to imagine the junction of the spikes and grooves in three dimensions. With square bars, this generally does not cause difficulties, but when the quarters go, you need to strain a little. I did not master AutoCAD, so I had to keep the whole isometry during the work. Otherwise, only patience is required. The second batch of windows I got much faster. Between these two parties there was a couple of windows that were simpler and smaller: just a dull window with one quarter where a double-glazed window is inserted. I made these three days in general: the first day - to grind and glue (two hours), the second day - quarters, spikes, grooves, assembly, grinding (five hours), the third day - impregnation (two hours).
In the store you can buy wooden window structures, PVC windows and aluminum profiles. Each of the materials has its own characteristics that can satisfy any customer requirements. But if we are talking about a window for a summer residence, then the most suitable option would be a wooden frame. Such a wooden window frame can be made in the presence of the necessary materials and tools, as well as in compliance with the technology. Work must be done carefully and accurately so that all geometric dimensions are clearly observed. The window will last a long time.
Structurally, a wooden frame can be made of several modifications:
In this case, in option 1, a window can be provided that will perform the ventilation function more efficiently than the sash.
The wooden frame can be made of any wood species. It all depends on personal preferences, skills in wood processing. The strongest and most durable breed is oak. Moreover, it is quite difficult to process and is an expensive material. Among other species that are most often used for the manufacture of wooden frames, birch, ash, pine, larch are known.
In order for the wooden frame to be strong and reliable, it is not necessary to take solid bars or boards. A very suitable material is glued beams. It is designed in such a way that it does not shrink during operation. This indicates a greater reliability and durability of this material.
As an alternative to wood, plywood sheets are used for the manufacture of a window wooden frame. It has sufficient strength and reliability, which allows its use as a source material.
The wooden frame can be assembled using the following tools:
Back to the table of contents
Before the wooden frame will be assembled, it is necessary to treat the bars with a special antiseptic composition. Thanks to this, the frame will last longer, since the wood will be protected from the formation of fungi and moisture.
Do-it-yourself frame making begins with the box. A slit is made in a board 50x150 mm in size so that a configuration in the form of the letter “G” is formed. This will ensure the tightness of the window. Next, divide it into 4 identical parts. They are fastened together by means of a tongue-and-groove connection. That is, on one of the parts a groove is sawn, and on the other a tenon is sawn. These 2 connection elements must be carefully dimensioned so that the spike enters the groove without gaps, stretching. This will ensure a secure fit.
The groove is performed using a circular saw, which make cuts. And the excess is removed with a chisel and a hammer. The spike can be made with both a hand saw and a circular saw, with a certain skill. Grooves should be made on the details of the frame, which are located vertically. On horizontal - spike is cut.
After preliminary assembly of the box elements, it is disassembled. Joiner glue is carefully applied to the fasteners. Then they are connected, strictly observing the geometric angle of 90 °. This can be controlled using a square.
After that, corners of metal are inserted at the end angles. They will provide the box with additional rigidity. Further work can only be done after the glue has completely dried.
The window wooden frame is made of timber with a section of 50x50 mm. From it you should cut the profile according to the design of the window. It will differ depending on the size and size of the glasses that will be inserted next, the width of the glazing bead. Wherein dimensions frames should be such that when it is inserted into the box, a gap of 1-2 mm is maintained. The profile is performed using an electric or manual planer. The resulting notches should be sanded with a machine or sandpaper.
The blanks of the wooden frame are fastened together like a box, that is, a thorn-groove connection is used. For reliability and rigidity glued. On the outside, at the corners, metal corners can be screwed, which, in addition to decorative purposes, will increase the rigidity of the structure.
After that, the wooden frame and box can be coated with stain and varnish, if you want to preserve and emphasize the texture of the wood, or paint. Hinges are screwed on the window frame and the box, which serve as a connection between these parts. After inserting the glasses, the frame can be hung on prepared hinges.
Wooden windows have always been popular due to such positive properties of wood as: high heat-saving characteristics, environmental friendliness and durability.
One of the advantages is also that manufacturing wooden windows do-it-yourself task is quite doable even for the layman.
Of course, now they use metal-plastic ones, which are cheaper and also have their indisputable advantages, but still wooden windows are a classic and they will always be popular.
The most popular material for the manufacture of wooden window cases in our latitudes is pine. It is distinguished by availability, low price and practicality. Oak is superior to pine in material characteristics, but it is more expensive and therefore, for the first time, it is better to stay on pine windows.
Process of creation
The basic requirements for the board are as follows. Firstly, it should be well dried, and secondly, not have knots and deformations. These conditions are important, since the box will experience the main load, so its strength should not be in doubt.
The manufacturing technology of wooden windows with their own hands, involves the use of glued beams for the implementation of the box. In this case, the box has the most robust design. Glued beam is the compilation of individual boards in packages and gluing them on a plane. Boards in our case will be made of pine.
The size of the board is taken 15 * 5 cm. They are connected together by gluing. Then four holes are drilled and wooden pins are inserted into them. Such a connection will provide structural rigidity. In the opening, the box is installed motionless, using self-tapping screws and dowels, and then, the cracks between the opening and the box are blown with mounting foam.
We need to briefly dwell on the tool that will be needed to make the window.
If the window will be made for a summer residence in which you do not live in the autumn-winter period, it will be enough to limit yourself to a thin double-glazed window.
Window frames
Helpful information:
Pay attention to inexpensive windows made of wood "Red Hill": a frame of two-layer glued beams (pine) 57x60 mm, single-chamber double-glazed window.
If you decide to manufacture wooden windows with double-glazed windows, then you need to start with the design of the window frame. The minimum beam that you will need in order to make a frame should be 6 * 4 cm and will depend on the thickness of the window.
The profile for one window pane should have two rectangular folds, and the window with two panes should have one more. Frame production begins with a thorough processing of the timber. Then, using the thicknesser, we do all the markings, after which we begin the device of folds (grooves).
The manufacture of folds is carried out so that when the frame is already assembled, they are in the same plane. Otherwise, the glass will be poorly sealed. In general, the dimensions of the grooves depend on the thickness of the glass and the type of sealant.
Note!
If putty is used as a seal, the folds have a smaller width than when using glazing beads.
It must be remembered that strongly narrowed folds will let wind through. The thickness of the grooves is also affected by the width of the strapping beam.
The window frame is assembled so that the spikes fit snugly into the grooves. For a tighter connection, a spike should be installed. To do this, you must first drill a hole along the diameter of the tenon and grease it with glue.
In addition, at the end of the frame boards, to improve the connection, you can use the key. Her appearance will resemble a double dovetail. To do this, at each of the ends to be connected, a hole is made in the form of a trapezoid, into which a key is then inserted. Before finishing the assembly, the joints are lubricated with glue, and after assembly, the remaining glue must be cleaned with a knife. In the manufacture of a window with a sash, the installation of accessories will be added to the above works.
To prevent the window from being blown, carefully adjust the glass to fit the frame. To do this, you need to carry out its cutting with a diamond glass cutter. Before work, for safety, you need to wear glasses to prevent glass chips from getting into the eye and mittens, so as not to cut your hands. Glass cutting is carried out with a ruler, which should exceed the length of the glass. After we have drawn the line with a glass cutter, we move the glass to the edge of the table and break off the excess with the help of pressure. Glass should break off by cutting.
Everyone who has an idea of \u200b\u200bhow to make wooden windows should know how to correctly insert a window into the frame. First, let's try chopped glass by inserting it into the frame. If the glass is cut correctly, then pull it out and begin to prepare folds.
To do this, they need to apply sealant and insert glass into the frame. We fix the glass with the upper glazing bead and fix it with a thin clove. When using a larger glazing bead, for its fastening to the frame, self-tapping screws can be used.
In the manufacture of windows, which consist of two halves, one more beam is installed in the center, with the same grooves. One half of the window is made with a thinner frame and attached to the main one using hinges. In addition, a handle is attached to such a frame, and a groove for the closing mechanism is cut out.
Double wooden window
Window leaves in wooden windows are an integral part and can be of several types: mortise, cut and sliding. The latter represent a rather complex mechanism and it is difficult to carry them out independently. The first option is made together with the window frame and maximum precision is needed here.
The best option for window leaves in wooden windows are split, which are made separately from the window, and then, ready-made, inserted into the frame.
Note!
When manufacturing a split window, it is not required to use any special fasteners or special skills during execution.
The manufacturing technology of such windows is slightly different from the mounting order of the window itself, only for smaller sizes. The difference is in mounting the opening mechanism, which usually represents the hinges, and attaching additional accessories, in the form of a handle with a closing device.
After completing all the work, the manufacturing technology involves lubricating the window surfaces with an antiseptic. After that, the window is placed in the opening and fastened in the grooves. Then we mount with screws that pass through the box and fasten them to concrete. Holes in concrete are made, most often, using an assembly gun.
After we fixed the window, we blow the cracks out with sealant. It is necessary to wait for it to dry, and then plaster the places of sealing. Work is being completed by mounting the ebb and window sill. Thus, it can be seen that making a wooden window with your own hands is not an impossible task, and this distinguishes them from metal-plastic windows.