I must say that the problem of how to manually tamp rubble can be quite relevant in private construction. No, of course, we are not talking about global projects, such as, for example, ramming a crushed stone cushion under the foundation of a house with an area of over 100 square meters. m. here you will definitely need special tools in the form of an asphalt roller or a building vibrating plate, since the amount of work is too large, and it will resemble a “manual sunset”. Let's talk about small forms: a parking lot in the country, a path in the garden, or the like. When you can really cope - and this is real and verified by the experience of many - on your own, without resorting to the help of expensive teams!
How to manually compact crushed stone? The problem is not easy: in a sense, physically. Its technical resolution has several options, invented by our mighty inventive and savvy people. We will talk about them in our article today, but first - about some general principles rammers.
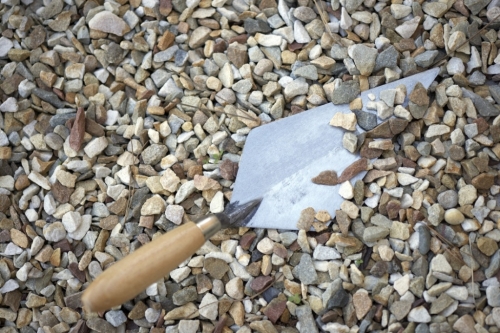
Why do you need to ram gravel?
Frankly, the problem is quite interesting and not entirely clear to some. And among beginners in the construction business, this is the most common question. It would seem that he covered the surfaces with this durable and strong material, leveled it and that's it - you can cover it with a final coating, what can happen, because a stone is a stone?
But not everything is so simple. As you know, crushed stone is not a simple, natural stone (like gravel), but artificially crushed. It is durable, but
sharp corners due to the technology of its production. Thus, additional tamping of the material creates a tighter fit of individual fractional fragments to each other, and excessive voids between them disappear or are reduced in volume. This creates an additional margin of stacking strength.
Let's hear the opinions of professionals. They confirm that tamping of crushed stone during construction is a must.
Exceptions may be such options when the natural soils on which the work is carried out are rocky. Then it will be sufficient to carefully level the rubble before the subsequent laying of concrete, tiles or asphalt on it. In all other cases, the idea is this: crushed stone as a base should not just lie in the ground, but form with it such a mixture compacted by tamping with dense filling of the cracks between the fractional fragments with soil. The thickness can vary for various purposes from 50 to 250 or more mm (this depends on what load the final coating will experience in the future). Now that with the theory - why tamping is necessary - more or less everything is clear, we move on, so to speak, to practical exercises.
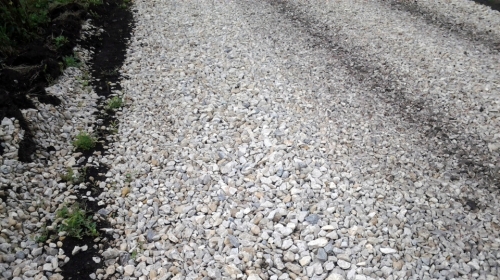
Manual rammer
When a vibrating plate and a roller are not at hand, tamping tools can be made by hand. But we repeat, these mechanisms set in motion
muscle strength of a person, invented by craftsmen, are relevant only for tamping not too large fragments of surfaces, or those that subsequently will not experience too powerful loads on themselves.
There are quite a few options on how to make a device for manual tampering. The simplest one looks like this. We take a wooden beam with a section of at least 100x100 mm, or better - 150x150, then we get a wider grip on the rammed surface. The height of the beam should be convenient for work (usually - about the chest of the person performing the tamping).
From a bar rounded 50x50 mm we make handles, which we nail to the base with nails and fasteners made of iron or galvanized sheet. We also sheathe the bottom of the fixture with a galvanized sheet to increase strength. In principle, the simplest device, probably known back in the time of the pharaohs, is ready for use. Of course, the surface area for tamping was not too large for him, but with free time and desire, they can even tamp a crushed stone pillow under the foundation, for example, of a small outbuilding.
True, it will take more time and effort than when using a gasoline vibrating plate, but as an option, it is actually quite widely used. Using such a manual mechanism is quite simple, however, a certain physical preparation is required, because you really get tired. We lift the device by the handles and forcefully lower it, for example, onto a garden path covered with rubble. We repeat the movement many times, moving in a given direction. Thus, you need to go all the way several times.
One note: There are many variants of such a device. There are more durable ones made of a metal pipe of about the same diameter with a metal “leg” welded to the base. True, this design creates too much vibration when used (which, for example, a wooden device dampens), and then work should be done with special gloves.
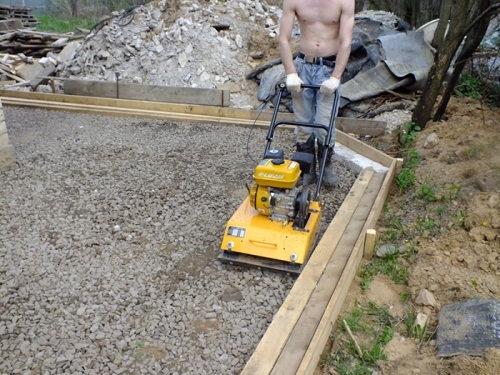
Do-it-yourself ice rink
The same applies to a manual asphalt roller, which is also used with might and main for compacting small fractions of crushed stone (especially for various track options). It is not difficult to make it, in the presence of a grinder and a welding machine, as well as certain materials. We cut a metal pipe with a diameter of at least 30 cm to a length of a meter. On the one hand, we brew with a metal sheet and cut it in a circle with a grinder. Exactly in the middle of the sheet there should be a hole for attaching the handle later.
We turn the pipe over with the open end up and pour sand inside. We also weld the other end with a sheet and cut it around the circumference. We put a handle from a curved pipe on the device for manual tampering. It turned out to be a universal device that, due to its weight, can be used for compacting small gravel, and for laying asphalt in the yard, and for sand and soil to make them denser. Using it is quite easy, but it will also require some skill and good physical development from you.
More options
If, for example, you need to tamp a small area for parking your car in the country, then you can use the following method, invented by the people and successfully used, since there is nothing particularly complicated in the technology. So, we scatter crushed stone over the territory measured in advance and marked with pegs (be sure to leave some of it for backfilling).
Level with a shovel so that the layer is the same thickness everywhere. Then we sit behind the wheel of a car and methodically begin to park in the future parking lot in various places - either in the center, then to the left, then to the right, then sideways - trying to cover the space covered with rubble as much as possible. We do the procedure many times (20, 30, 50) until we make sure that the rubble is compacted over the entire plane by the weight of the car. Shallow ruts may appear in some places. We pour pre-prepared crushed stone into them and continue. This is so simple, but effective way, however, not quite manually, but using the weight of your car.
A well-prepared base is the result of the durability of the industrial floor and the building as a whole. Soil compaction methods are different, one thing remains similar - the use of special compaction equipment. The soil is compacted to increase the ability to withstand heavy loads. The principle of operation is based on the displacement of air. At maximum compaction, its content is not more than 3-5%.
When installing a concrete floor slab on a soil base, it is necessary to carry out work on planning the existing soil base. Peat, vegetable soil, construction waste must be removed. Clay soils also need to be removed to a depth of about 0.5 m. This is necessary to create a "trough", which is subsequently filled with sand and gravel to create the bearing capacity of the base. Removal of sandy soils is not required. Sandy soils consist of small particles 0.1-2 mm in size. Dense sand is an excellent foundation for building structures because it has a low compression ratio.
Depending on the loads acting on the soil base, a calculation is made. Depending on the loads, the thickness of the sand, crushed stone bedding, and sandy stone bedding is determined. The fraction and material of crushed stone, soil compaction coefficient, etc. are also determined.
Sealing methods.
To select a compaction method, you need to know several parameters - humidity, degree of uniformity, desired density of sand or gravel, season, and so on. Compaction is carried out only with a certain percentage of sand moisture, therefore, if necessary, the soil is moistened with watering hoses. Frozen soils cannot be compacted. Before the start of the compaction phase, a test compaction is carried out. Typically, the test section is no larger than 3dx3d, where d is the diameter of the rammer.
The main methods of soil compaction:
- rolling - using rollers
- rammer
- vibrotamping
Very often several methods are combined.
During rolling, static pressure is transferred from the roller to the ground. It is carried out by self-propelled and trailed rollers. The thickness of the compacted layer is 35-50 cm. Several passes are required in the same place.
Conventional ramming is based on the transfer of the impact force from the discarded compactor (large mass plate) to the ground. This method has a large load, which ensures the compaction of crushed stone and sand to a depth of 2 m. It is carried out using tamping plates weighing 1-2 tons, which are dropped from a height of 1-2 m. sand in small quantities.
The most common soil compaction method is vibrotamping. This method is based on the transmission of mechanical vibrations. Vibrocompaction is carried out by vibratory rollers, self-propelled vibrorammers and vibrating plates. The thickness of the compacted sand or gravel is 30-50 cm.
Works on the device of sand preparation are carried out in layers, with obligatory compaction by vibratory rollers, and in places near walls and columns by vibrating plates and vibrorammers. The compaction coefficient of sand preparation should be at least 0.95. The upper layer of preparation is usually made of crushed stone of a fraction of 40-60 mm, followed by buckling with crushed stone of a fraction of 5-20.
In the case of shallow groundwater, the crushed stone base must be separated from the floor slab (to exclude the rise of water vapor) using a polyethylene film (two layers of 200 microns each) or a waterproofing membrane.
All materials for the preparation of the base must comply with GOST. The resulting base should not have differences of more than 20 mm over the entire area. Compaction of crushed stone and sand increases the strength of the soil, reduces compressibility. The process is mandatory to ensure the strength of the base and foundation.
The average cost of work on the preparation of the soil base.
№
|
Name of works |
Price |
1
|
Selection of an earthen trough with subsequent removal and planning of the territory under the mark |
450 rub/m 3 |
2
|
Sand base with 50 mm thick seal
|
90 rub/m2 |
3
|
Crushed stone foundation with 50 mm thick crushed limestone compaction |
180 rub/m2 |
4
|
Sand base with 100 mm thick seal |
140 rub/m2 |
5
|
Crushed stone foundation with 100 mm thick crushed limestone compaction |
280 rub/m2 |
MINISTRY OF TRANSPORT CONSTRUCTION
STATE ALL-UNION ROAD SCIENTIFIC RESEARCH INSTITUTE
Approved by the Director of Soyuzdornia, Candidate of Technical Sciences E.M. Dobrov
Approved by Glavdorstroy
(Letter No. 5603/501 of 08/01/83)
Moscow 1985
Designs of crushed stone bases treated with sand-cement mixture developed by Soyuzdornia, Giprodornia and Gosdornia, a method for determining the calculated modulus of elasticity of the layer are given; requirements for sand-cement mixture and crushed stone treated with sand-cement mixture. Recommendations are given for the selection of mixture compositions that provide the required strength and frost resistance of the base layer; according to the technology of building a crushed stone base, treated in the upper part with a sand-cement mixture by two methods: the mixing method using a profiler and the indentation method using a vibratory roller, a cam roller and a roller on pneumatic tires. The need for quality control of construction is indicated. 2, tab. 8.
Foreword
The pace of pavement construction is constantly growing. The urgency of the task is increasing - to develop a base design using local materials and propose an appropriate technology that would improve quality and efficiency, as well as accelerate the construction of bases with increased bearing capacity. research and experimental works of Soyuzdornia, Giprodornia, Gosdornia and the construction of experimental sites by the Magistraldorstroy trust of Glavdorstroy and other organizations. These "Methodological recommendations" describe the design and construction technology of a crushed stone base treated in the upper part with a sand-cement mixture or other inorganic binders .The proposed design of the base and the technology of its device allow: to increase the bearing capacity in comparison with the widespread crushed stone and gravel bases and to reduce by 10 - 20% material consumption. reduce cement consumption by 10 - 20% due to the processing of coarse-grained materials compared to fine-grained materials with a smaller amount of binder; and soil cement; to lengthen the construction season due to the removal of crushed stone in winter and the final arrangement of the foundation in summer, which leads to a decrease in the need for vehicles in the summer; to use mixing plants of small capacity for high-speed construction of foundations due to a smaller volume of mixed material; to reduce by 10 - 20% fuel consumption by reducing the volume of transportation by road compared to transportation during the construction of traditional crushed stone or gravel bases; reduce labor and energy costs for mixing the mixture due to the smaller amount of work at the mixing plant. The net economic effect from reducing material consumption, reducing the consumption of binder and fuel and energy resources during the construction of 1 km of foundation is approximately 1 - 6 thousand rubles. The novelty of the work is protected by copyright certificates: No. 903446, No. 960348, No. " were made by candidates of technical sciences V.S. Isaev, V.M. Yumashev, A.O. Sall, I.Z. Dukhovny, O.N. Rudaya, engineers N. A. Yorkina, M.F. Fomina, V.M. Beskrovny, V.M. Belousov, E.V. Volkov.
1. General Provisions
1.1. These Methodological Recommendations have been developed in the development of SNiP II-D.5-72 and SNiP III-40-78 and are intended for use in the construction of crushed stone bases treated in the upper part with a sand-cement mixture or inorganic binders based on production waste (metallurgical slag, belite sludge, active fly ash, etc.). 1.2. The crushed stone layer should be treated with a sand-cement mixture using the mixing method and the impregnation-indentation method. When using the mixing method, the required processing depth is provided by setting the working bodies of the DS-108 profiler, which distributes the layer of crushed stone and sand cement with a screw-cutter, and then mixes them. When using the impregnation method - the indentation depth of processing depends on the voidness of the crushed stone layer and the machines used - a cam roller, a vibratory roller, a roller on pneumatic tires. 1.3. The base of the developed structure must be arranged on the subgrade or underlying layer adopted by the act. 1.4. The length of the interchangeable grip should be determined based on the planned pace of construction and the availability of machines and mechanisms. 1.5. Crushed stone bases treated with a sand-cement mixture or other binders should be installed in dry weather at an average daily air temperature of at least 5 ° C. Crushed stone is allowed to be taken out in winter to intermediate warehouses to the place of future construction. 1.6. Foundation work must be carried out in accordance with the "Safety regulations for the construction, repair and maintenance of highways" (M.: Transport, 1978) and SNiP III-A.11-70 "Safety in construction" (M.: Stroyizdat , 1972).
2. Pavement base structures
2.1. The average modulus of elasticity of the base structure with a modulus of elasticity variable over the depth of the layer can be determined by conditionally dividing the base into two parts: the upper, treated with a sand-cement mixture, and the lower, untreated, with the corresponding design parameters shown in Fig. 1 and in table. one.
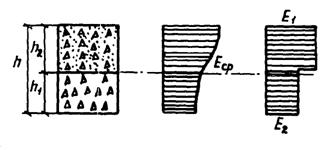
Rice. 1. Diagram of the modules of the structure of the crushed stone base, treated in the upper part with inorganic binders: h - total thickness of the base, cm: h 1, h 2 - thicknesses of the upper processed and lower untreated parts of the base layer, cm; E 1, E 2- moduli of elasticity of the treated and untreated parts of the base layer, MPa; E cf - average modulus of elasticity of the base layer, MPa
When designing, it must be borne in mind that the bearing capacity of the structure of a crushed stone base, treated in the upper part with a sand-cement mixture, characterized by an average modulus of elasticity of the layer Eav, depends on the values of the modulus of elasticity of the treated E 1 and raw E 2 parts and their thicknesses h 1 and h2(see Fig. 1) with a total layer thickness h.
Table 1
Layer Height Ratio h 1
/
h
|
Modulus of elasticity of the untreated part E 2 , MPa
|
The value of the average modulus of elasticity of the base E cp, MPa, equal to at E 1, MPA, equal to
|
|
|
|
|
|
|
|
|
|
|
|
|
|
|
|
|
|
|
|
|
|
|
|
|
|
|
|
|
|
|
|
|
|
|
|
|
|
|
|
|
|
|
|
|
|
|
|
|
|
|
|
|
|
|
|
|
|
|
|
|
|
|
|
|
|
|
|
|
|
|
|
|
The value of the average modulus of elasticity of the base layer E cf when calculating according to the "Instructions for the design of non-rigid pavements" VSN 46-83 (M. according to the table 1.2.2. The calculated modulus of elasticity of the lower, untreated part of the base, depending on the properties of the materials used, must be taken according to the "Instructions" VSN 46-83 with the additions given in Table. 2 of these "Guidelines".2.3. The calculated modulus of elasticity of the upper, treated part of the base, depending on the strength grade of the sand cement used and its amount in the crushed stone layer, providing different strength grades of the treated material that meets the requirements of GOST 23558-79, should be taken from Table. 3.
table 2
Grade for the strength of crushed rock
|
Estimated modulus of elasticity of the raw part, MPa, with crushed stone size, mm
|
carbonate
|
igneous
|
sandstone
|
|
|
|
|
|
|
|
|
|
|
|
|
|
|
|
|
|
|
|
|
|
|
|
|
Table 3
Resistance of sand cement to compression, MPa, at a ratio of W: PC, % (K section)
|
Indices of the properties of the processed material
|
|
|
|
Modulus of elasticity, MPa
|
|
Bending tensile strength, MPa
|
|
|
|
|
|
|
|
|
|
|
|
|
|
|
|
|
|
|
|
|
|
|
|
|
|
|
|
|
|
|
2.4. The minimum total thickness of the base layer should be at least 10 cm, the maximum - no more than 25 cm. The maximum grain size of crushed stone should not exceed 2/3 of the thickness of the base. cam roller should be no more than 15 cm, and with the use of rollers on pneumatic tires and vibration - no more than 7 cm.
3. Requirements for the materials used
3.1. The stone materials used for the device of the proposed design should be subject to requirements for strength, frost resistance and grain composition. For a mixture of sand with cement or other inorganic binder, requirements should be imposed on composition, strength and frost resistance, 3.2. The strength of crushed stone from natural rocks must meet the requirements of GOST 8267-82, the strength of slag crushed stone - GOST 3344-73.3.3. Frost resistance of crushed stone must meet the requirements given in table. 4 of these "Guidelines".
Table 4
|
Climatic conditions
|
Grade of crushed stone in terms of frost resistance, not less, for
|
grounds
|
coatings
|
|
severe |
|
Do not apply
|
Moderate |
|
Soft |
|
|
severe |
|
|
Moderate |
|
|
Soft |
|
|
3.4. When constructing the foundation by mixing, it is advisable to use crushed stone of a fraction of 5 - 40 (70) mm, by impregnation-indentation using rollers on pneumatic tires - crushed stone of a fraction of 40 - 70 or 70 - 120 mm. When using cam and vibratory rollers, it is also advisable to use crushed stone with a fraction of 20 - 40 mm. 3.5. The content of weak and weathered rocks in crushed stone should not exceed 15%, grains of lamellar (flaky) and needle-shaped grains in crushed stone should not be limited, dust-like and clay particles should be no more than 4%, including lumps of clay particles larger than 5 mm - 2% .3.6. Losses in mass during testing of crushed slag for structure stability should not be more than 7%. 3.7. For processing crushed stone, you can use sand-cement, sand-slag (based on crushed ferrous metallurgy slag and cement activator) and sand-ash mixture (based on ashes and slags from thermal power plants), as well as non-crushed granulated blast-furnace slag and belite sludge. 3.8. The mixtures listed in clause 3.7 must meet the requirements of GOST 23558-79. Compression resistance of sand cement at the age of 28 days, and slag and sludge at the age of 90 days. must be at least 3 MPa. In each specific case, the brand of samples from the mixture should be assigned so as to obtain the required strength (calculated modulus of elasticity) of the treated part of the layer and the entire base structure as a whole according to Table. 3. The composition of the sand-cement mixture is determined in each case by laboratory selection. 3.9. The frost resistance of sand cement, determined according to GOST 23558-79, must meet the requirements given in Table. 5.3.10. Cement for sand-cement mixture must meet the requirements of GOST 10178-76. The beginning of cement setting is not earlier than 2 hours after mixing. It is recommended to use Portland cement and Portland slag cement grades 300 and 400.
Table 5
|
Climatic conditions
|
Grade of sand cement in terms of frost resistance, not less, for
|
the bottom layer of the base
|
the top layer of the base
|
coatings
|
|
severe |
|
|
Do not apply
|
Moderate |
|
|
Soft |
|
|
|
severe |
|
|
Moderate |
|
|
Soft |
|
|
|
severe |
|
|
|
Moderate |
|
|
|
Soft |
|
|
|
3.11. Granulated blast-furnace slags or slag fines with an activity of more than 5 MPa according to GOST 3344-73 and a maximum particle size of 5 mm can be used as a wedging and binding material in the proposed design. 3.12. Instead of a sand-cement mixture, alumina production waste can be used for processing crushed stone - belite (nepheline or bauxite) sludge with the following characteristics: 40 - 85 Bulk density, kg/m 3 900 - 1200 Natural humidity, % 15 - 30 Optimum humidity, % 20 - 25 Compressive strength of sludge at the age of 90 days, MPa, not less than 33.13. The sand must meet the requirements of GOST 8736-77 with the following additions. The content of dusty clay and silt particles, determined by elutriation, should not exceed 8% in natural sands, 10% - crushed from screenings, including the content of clay in lumps should not exceed 2%. The content of particles less than 0.14 mm in natural sands should not exceed 30%, in crushed carbonate rocks from screenings - 40%. The number of plasticity of sand fractions finer than 0.63 mm should not exceed 2.3.14. When processing crushed stone with a fraction of 70 - 120 mm, it is allowed to use a sand-gravel mixture and crushing screenings with a maximum fineness of 20 mm. When processing crushed stone with a fraction of 40 - 70 mm, there should not be grains larger than 10 mm in the sand, when processing crushed stone with fractions of 20 - 40 mm - larger than 3 (5) mm. 3.15. For the preparation of mixtures and watering of crushed stone, it is recommended to use water suitable for drinking. 3.16. To reduce cement consumption by 10 - 15% and improve the technological properties of sand cement (increase mobility), SDB should be introduced into the mixing water in an amount of 0.5 - 1% of the mass of cement. SDB consumption is specified during laboratory selection of the composition of the sand-cement mixture from specific materials.
4. Technical and economic choice of the pavement base
4.1. Depending on the depth of impregnation, as well as the required average modulus of elasticity of the base layer, the base structures shown in Fig. 2.4.2. The base design must be selected on the basis of a technical and economic comparison of options, taking into account the cost of materials and the composition of the mixture. , rub.; l, in - length and width of the section, respectively, m; h 2 - thickness of the lower, untreated part of the layer, K ysh - crushed stone compaction coefficient; K p - loss coefficient, K p \u003d 1.03; h 1 - the thickness of the upper, processed part of the layer. m;
ρ shpc- average density of a mixture of crushed stone with sand cement, t / m 3; - the content of crushed stone in the upper, processed part of the layer, fractions of a unit;
ρ n- bulk density of crushed stone, t / m 3. The cost of the sand-cement mixture is determined by the formula:
where, - the cost of 1 m 3 of sand and 1 ton of cement, respectively, rub.; - the content of sand cement in the mixture, it with crushed stone, fractions of a unit;
ρ pts- average density of sand cement, t/m 3 ;
ρ np- bulk density of sand, t / m 3; - the content of cement in sand cement, fractions of a unit; - sand content in sand cement, fractions of a unit. 4.3. Since the cost of crushed stone is most often 3 - 8 rubles, and sand - 2 - 5 rubles. per 1 m 3, the best design option from those shown in fig. 2 is reasonable to accept, taking into account the following: while maintaining a constant total thickness of the structure, the average modulus of elasticity and the ratio of the thicknesses of the upper and lower parts of the layer, it is more economically advantageous to use a material with a high modulus of elasticity in the lower layer, and low-quality processed materials in the upper layer; while maintaining a constant average modulus of elasticity and the total thickness of the base layer with an increase in the modulus of elasticity of the upper processed part of the layer and a decrease in the depth of impregnation, the cost of the structure decreases; while maintaining a constant depth of impregnation with an increase in the average modulus of elasticity (with a decrease in the thickness of the base), the cost of the structure decreases; the upper part with a sand-cement mixture, it is more economical than an equal-strength base completely made of these materials (at their equal costs). for 1 m 3.
5. Foundation design
5.1. For the design of bases, the following are required: the required modulus of elasticity of the base structure; the required frost resistance of crushed stone and sand cement; base thickness; crushed stone characteristics (grain composition, strength, frost resistance, original rock); sand characteristics (size modulus, type of sand by origin); cement brand; mechanisms for impregnation and the depth of impregnation of crushed stone with sand cement adopted in accordance with this. 5.2. When designing foundations, you should: determine the required modulus of elasticity of the upper, processed and lower parts of the layer that are not processed according to the "Instructions" VSN 46-83 for a given general modulus of elasticity of the structure and the depth of impregnation, as well as with known characteristics of crushed stone; determine (based on the modulus of elasticity ) the required strength of the upper, treated part of the layer; determine the required strength of sand cement, providing the required strength of the treated part of the layer; check whether the frost resistance of sand cement meets the specified requirements; determine the amount of binder in the sand-cement mixture of the required strength; determine the required amount of water in the sand-cement mixture per unit area of the structure ; determine the amount of water required for irrigation of a unit area of the crushed stone layer; establish the amount of sand-cement mixture required to impregnate the crushed stone of a given grain composition to the accepted depth per unit area of the structure; determine the consumption of crushed stone, sand and cement for unity area of the designed base structure.5.3. The required modulus of elasticity of the upper, treated part of the layer can be determined by the formulas: where E cf is the design average modulus of elasticity of the structure, MPa; tab. 2 of these "Guidelines" depending on the strength, grain composition and rock of the crushed stone planned for use, MPa;
h1- thickness of the upper, processed part of the layer, m; is accepted according to the assignment, taking into account the requirements of these "Guidelines", depending on the intended construction technology; h 2 - the thickness of the lower crushed stone part of the layer, m; is taken according to the assignment, based on the total required thickness of the base. The value of the modulus of elasticity of the upper, processed part of the layer for the most common values of the average moduli of elasticity of the layer and the modulus of elasticity of crushed stone layers can be found in Table. 1 of these "Guidelines".5.4. The required strength of the upper, treated part of the layer can be calculated from the correlation between the strength R com (MPa) and the elastic modulus E 1 (MPa) of this material: tab. 3 of these "Guidelines".5.5. The required strength of sand cement or other binder, which provides the necessary strength of the treated part of the layer R gpc, should be calculated from the dependencies:
2.08 R nib + 0.3 at W: PC = 80:20,
1.1 R pinch + 0.8 at SC: PC = 65:35,
1.2 + 1 at W: PC = 50:50.
|
|
You can set the grade of sand cement for strength (compression resistance) required to provide the required grade for the strength of the treated part of the layer at various ratios of crushed stone and sand cement, according to Table. 3 of these "Guidelines".5.6. Sand cement with characteristics calculated in accordance with the requirements given in paragraphs. 5.8 - 5.5 should be checked for frost resistance. The requirements for frost resistance of sand cement for specific climatic conditions of construction, the category of the road and the layer of pavement are given in Table. 5 of these "Guidelines". Roughly, the frost resistance of sand cement, depending on its strength grade, can be calculated using the following correlations:
Finally, the frost resistance of sand cement is determined experimentally in the laboratory in accordance with GOST 23558-79. If sand cement with the required strength grade does not meet the frost resistance requirements given in Table. 5 of these "Methodological recommendations", then experimentally select sand cement with the necessary strength, which also meets the specified requirements for frost resistance. After that, if necessary, recalculate the structure with a new grade of sand cement. 5.7. Consumption of cement brand 400p c (%) to obtain sand cement of the required grade in terms of strength at the age of 28 days R c, (MPa) can be approximately calculated from the following correlation dependencies: When using sands of different grain composition and nature, the approximate consumption of cement grade 400 can be taken from . 6 of these "Methodological recommendations" and specify in the laboratory selection of specific materials in accordance with the requirements of GOST 23558-79. In this case, three series of samples with different amounts of cement should be prepared.
Table 6
The amount of cement,%, required for processing
|
Compression resistance of sand cement, MPa
|
screenings crushing carbonate rocks
|
coarse and medium grained sands
|
fine sands
|
|
|
|
|
|
|
|
|
|
|
|
|
|
|
|
|
|
|
|
|
|
|
|
|
|
|
|
|
|
|
|
|
When using cement grades 300 and 500 indicated in table. 8 the quantity should be changed using coefficients of 1.2 and 0.9, respectively. When using slag and ash binders according to GOST 23558-79 strength grades 50, 100, 150, their number should be increased by 3; 2; 1.5 times compared with the data in Table. 6. Slags, ashes and sludge with an activity of at least 5 MPa at the age of 90 days. can be used as an independent binder. To increase the strength of the treated part of the layer by 10 - 30% or reduce cement consumption by 10 - 20%, it is advisable to introduce SDB into the mixture in an amount of 0.5 - 1% of the mass of cement. 5.8. Sand cement of the highest strength at a given cement content can be obtained with the optimal amount of water in the mixture (approximately 7 - 10% of the mass of the dry mixture), which is established experimentally when selecting the composition of the mixture. should be calculated according to the formulas: where l, in - the length and width of the section, respectively, m;
h1- thickness of the upper, treated part of the layer, m; - the content of sand cement or other binder in the treated part of the layer, fractions of a unit;
ρ pts- density of sand-cement mixture, t/m 3 ; - the optimal water content in the sand-cement mixture, fractions of a unit; Qpc - the amount of sand-cement mixture, t. When arranging the base with vibratory rollers or rollers on pneumatic tires, the amount of water in the sand-cement mixture for its good penetration into crushed stone should be 3 - 5% less or more than the optimal one calculated by formulas (9) .5.9. In order to obtain the maximum strength of the layer of crushed stone treated with sand cement, before spreading the sand cement, the crushed stone should be moistened to create a mixture of optimal moisture (approximately 7 - 9% of the mass of the mixture). calculate according to the formula: 5.10. The amount of sand-cement mixture Qpc or other binders introduced into the crushed stone can be determined by the voidness of the crushed stone and the specified processing depth (thickness of the treated base layer) approximately according to the formulas:
,
Q pts \u003d lv h 1 ρ pts V psch K r K p,
|
|
or
Q pts \u003d lv h 1 ρ pts K p,
where ρ 1 - density (bulk density) of crushed stone grains, t/m 3; ρ 2 - bulk density (bulk density) of crushed stone in a compacted state, t/m 3; K r- coefficient of separation of crushed stone grains, K p = 1 ÷ 1.15; V n- voidness of crushed stone, fractions of a unit; K p - loss coefficient, K p \u003d 1.03. The value of ρ 2 can be determined by compacting 10 kg of crushed stone in a steel cylinder with a diameter and height of 234 mm with a load of 10 kg on a vibrating table at a vibration frequency of 3000 rpm min, amplitude 0.4 mm for 30 s. 5.11. When arranging the base by the method of impregnation-indentation, taking into account the depth of processing, fractionated crushed stone should be treated with 35 - 40% of the sand-cement mixture, which corresponds to the voidness of the material being laid. Crushed stone with a fraction of 5 - 40 mm when arranging the base by the mixing method, taking into account the depth of processing, it is advisable to process with a sand-cement mixture in an amount of 20 %, which also corresponds to the voidness of the mixture. It is allowed, during a feasibility study, to process crushed stone with 35 - 40 and 50% of the sand-cement mixture. Before starting work, to clarify the consumption of the sand-cement mixture, the voidness of the materials used should be determined and formulas (12) should be used. Estimated consumption of sand-cement mixture for a device of 100 m 2 of base at various depths of crushed stone processing, taking into account the surface layer of sand-cement 1.5 cm thick, is given in Table. 7 of these "Guidelines".
Table 7
5.12. After establishing the laboratory composition of sand cement, the need for materials per unit area of the base should be calculated. The required amount of crushed stone (m 3) can be determined by the formulas: The amount of sand (m 3) for the preparation of a sand-cement mixture should be determined by the formulas: where - the content of sand in the sand-cement mixture, fractions of a unit; ρ np - the bulk density of sand, t / m 3 .5.14. The amount of cement Q c (t) for the preparation of sand cement can be determined by the formulas: where is the content of cement in the sand-cement mixture, fractions of a unit. 5.15. In the course of work, the calculated composition of materials must be amended to take into account the actual moisture content of the materials. According to the formulas:
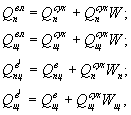
|
|
where W p, W sh - moisture content of sand and gravel, respectively, fractions of a unit; - the amount of water required to prepare a sand-cement mixture on wet sand, t; - optimal water content in the sand-cement mixture, t; - the amount of water required to prepare the mixture on wet gravel, i.e.
6. The technology of building foundations by mixing
6.1. When building foundations by mixing, crushed stone is taken out onto the prepared underlying layer, the amount of which should be determined taking into account the design thickness of the foundation and the compaction coefficient. In winter, crushed stone can be taken out to intermediate roadside warehouses in the area of planned construction. 6.2. Crushed stone is preliminarily distributed by a bulldozer or motor grader, and finally, to the design thickness of the base, taking into account the compaction coefficient, by a DS-108 type profiler or other distributors in one pass. When crushed stone is distributed by a profiler, the cutter and cutter blade are raised. The screw blade is set to the design mark with a margin for compaction. The auger is raised 2 - 2.5 cm above the cutting edge of the blade. 6.3. After distribution, the crushed stone, if necessary, before processing with sand cement, should be moistened to obtain the subsequent mixture of crushed stone with sand cement of optimal moisture content (approximate water consumption - up to 10 liters per 1 m 2) and rolled for the passage of construction vehicles (two - three passes of the skating rink along one track). 6.4. The sand-cement mixture intended for processing the upper part of the crushed stone layer must be prepared in mixing plants such as SB-78 or DS-50A. To ensure the qualitative composition of the mixture, it is necessary to supply sand with an accuracy of at least ±.5%, cement and water ±2% of the mass of the supplied material.6.5. The mixture should be transported by dump trucks or other vehicles and with an appropriate feasibility study.6.6. The sand-cement mixture must be pre-distributed with a motor grader, and finally laid on the surface of the distributed crushed stone with a profiler or other distributors. The consumption of sand cement is determined taking into account the given depth of processing of the crushed stone layer and the ratio between crushed stone and sand cement in the processed part of the layer. When planning, the auger and blade are raised to the thickness of the layer of the distributed mixture, and the cutter and blade of the cutter are raised to the transport position.6.7. At the end of the distribution, the sand-cement mixture must be mixed with the laid crushed stone to the calculated (required) depth. The maximum mixing depth for the profiler should not exceed 15 cm. Mixing is carried out at a working speed of 5 m/min. cutter at maximum speed and auger; at the same time, the blades are raised to the transport position, and the cutter and auger are set to the mark of the processing depth. If necessary, the resulting mixture is additionally moistened so that the mixture has optimal moisture content, and mixed again with one or two passes of the profiler. After mixing, the base is planned in one pass of the profiler. Working bodies are installed in the same way as when planning crushed stone. Working speed 7 - 8 m/min.6.8. The base immediately after mixing should be compacted in 12 - 16 passes of the roller on pneumatic tires in one track. In this case, the compaction coefficient at a depth of 5 - 20 cm should be at least 0.98. Seal starts from the edges of the base to the middle. 6.9. Compaction must be completed within 3 hours from the moment the sand-cement mixture is prepared, including the time for transporting the finished sand-cement mixture to the road section under construction, its distribution and compaction. -cement should not exceed 4 - 5 hours. When processing crushed stone with non-crushed granulated blast-furnace slag without cement activator or bauxite and nepheline sludge, the technological gap can be increased to 6 - 8 hours. 6.10. Upon completion of the compaction, the base should be finely finished with a profiler and the surface layer should be finally compacted with a heavy smooth-roller roller in one or two passes along one track. When finishing planning, the cutter and blade of the cutter are raised; the screw blade is set to the design mark; the auger is raised 1 - 2 cm above the cutting edge of the blade. 6.11. Upon completion of the final layout, it is necessary to care for the base by one of the generally accepted methods used in the care of cement concrete, in accordance with SNiP III-40-78. It is allowed to lay the coating on the day of the foundation; in this case maintenance of the base is excluded. 6.12. Opening traffic on the base, arranged using cement, should be after gaining 70% of the design strength of the base, but not earlier than after 7 days. after completion of work.
7. Technology of foundation construction by impregnation-indentation
7.1. The essence of processing a layer of crushed stone with a sand-cement mixture is to fill the voids of the crushed stone layer with a mixture under the action of its own weight and indentation during rolling (mechanical action), in several ways; pressure - rollers on pneumatic tires.7.2. Crushed stone before processing with sand cement should be carefully planned with a motor grader and poured with water in the amount of 3 - 10 liters per 1 m 2. If necessary, ensure the passage of construction vehicles, crushed stone is rolled with a light roller in two to four passes along one track according to SNiP III-40-78.7.3. The sand-cement mixture prepared in the installation must be distributed over the surface of the crushed stone layer by a profiler or motor grader. The consumption of sand cement is determined depending on the voidness of the crushed stone and the depth of the layer processing. The time of the technological gap between the preparation of the mixture and the end of the compaction is recommended to be taken in accordance with paragraph 6.9 of these "Methodological recommendations". 7.4. For processing crushed stone by vibration, it is recommended to distribute the sand-cement mixture with DS-97, DS-108, D-345 pavers equipped with vibration compacting bodies. In this case, at the same time, in one pass of the paver, the distribution and penetration of the sand-cement mixture into the crushed stone layer occurs. 7.5. To treat the crushed stone layer with vibration and pressure, a DU-54 vibratory roller should be used, the vibrating roller of which contributes to the penetration of the distributed sand-cement mixture into the voids of the crushed stone layer in three to four passes along one track. 7.6. To process the crushed stone layer by the method of deep pressure, it is advisable to use a cam roller, which in the process increases the gaps between individual gravel, providing an increase in the penetration depth of the sand-cement mixture into the crushed stone layer. It is recommended to use cam rollers of the DU-28, DU-3A or DU-32A type movement 4 - 8 km/h.7.7. Depending on the required thickness of the treated monolithic base layer, indentation can be carried out in two ways. With the required thickness of the monolithic layer of not more than 13 cm, it is recommended to press the sand-cement mixture or other binder into the crushed stone in successive passes of the cam roller, and with a thickness of more than 13 cm - alternating the passages of the cam and pneumatic or smooth-roller rollers through each pass. The approximate number of passes of the cam roller can be assigned in accordance with Table. 8 of these "Methodological Recommendations" and refined based on the results of a test indentation at the beginning of work.
Table 8
The indentation of sand-cement mixture or belite slurry into the crushed stone layer with a cam roller starts from the shoulders with the subsequent passages moving to the longitudinal axis of the highway and overlapping the trace of each previous passage by at least 20 cm. 7.8. To process a layer of crushed stone using the surface pressure method, rollers on pneumatic tires should be used, pressing the sand cement with two or three passes of the roller along one track. 7.9. The final compaction of the layer after processing the crushed stone by one of the previously mentioned methods should be done with rollers on pneumatic tires of the type DU-29, DU-16V, DU-31 in 12 - 16 passes along one track and in accordance with paragraphs. 5.42 - 5.46 of the "Technical Instructions" VSN 184-75. When using the indentation method by alternating passes of the cam and pneumatic or smooth-roller rollers, the number of passes of the pneumatic roller can be reduced to five to eight due to the fact that, simultaneously with the indentation, a partial compaction of the base occurs. The compacted base should be trimmed passages of a smooth-roller roller. 7.10. At the end of the compaction of the base, it is necessary to take care of it (see clause 6.11 of these "Guidelines"). 7.11. The movement of construction vehicles on the base can be opened after they have gained 70% of the design strength when processing crushed stone with a sand-cement mixture or slag binders with cement activator.
Vehicle can be opened immediately after the device. If on the next day after the installation of such a base it is not planned to lay the overlying layer, then the base must be maintained by watering it daily (in dry weather) with water in the amount of 1.5 - 2 liters per 1 m 2 during the entire warm period before laying the overlying pavement layer.
8. Construction quality control
8.1. All foundation materials should be checked for compliance with their standards for these materials. 8.2. The composition of the sand-cement or sand-slag mixture and its quantity per 1 m 2 of the base, ensuring the design strength of the mixture of crushed stone with sand cement, the laboratory must determine before construction begins by selecting materials. 8.3. The design composition of the sand-cement or sand-slag mixture should be controlled in accordance with SNiP III-40-78 using batchers at the mixing plant. 8.4. The quality of the prepared sand-cement (sand-slag) mixture should be controlled by making three samples in each shift and testing them for compressive strength at the age of 28 days. in accordance with the requirements and methods of GOST 23558-79 with the addition of an activator-cement to the slag, and at the age of 90 days. when using slag and sludge without additives. Bending strength (split), as well as frost resistance, should be determined on samples taken from every 5 thousand m 3 of the prepared mixture, in accordance with the requirements of GOST 23558-79.8.5. When spreading crushed stone and sand-cement or sand-slag mixture, as well as slag and sludge, the thickness and width of the layer of distributed materials should be controlled with measuring rulers and tapes for every 100 m of the base. The thickness of the layer in each diameter must be measured along the axis of the base and at a distance of 1 - 1.5 m from the edges. 8.6. The quality of mixing crushed stone with sand-cement. or sand and slag mixture, as well as with slag and sludge, or the quality of impregnation should be assessed by the depth of impregnation or by the amount of binder used. edges. The amount of sand-cement (sand-slag) mixture in a layer of crushed stone is recommended to be determined at least once per shift by taking a sample weighing 10 kg and then sieving it on a sieve with a hole diameter of 5 mm. 8.7. The technological gap between the preparation of the sand-cement mixture and the end of the compaction of the base, as well as the quality of the compaction, should be controlled in accordance with SNiP III-40-78.8.8. Compliance with the strength of the arranged base of the design one can be assessed by determining the modulus of elasticity with a deflection meter or other device. The modulus of elasticity must not be less than the calculated (design) one. 8.9. After completion of compaction and finishing, for every 100 m of the base, the evenness and transverse slopes should be checked with a three-meter metal lath and a template with a level. 8.10. After compaction of the base, it is necessary to monitor the timely pouring of film-forming material or water. Lack of care reduces the strength of the base by 50%. Reducing the care time (when watering) up to 21 days. from the moment of compaction of the base, it reduces the strength by 8 - 10%, up to 14 days. - by 20 - 25% and up to 7 days. - by 25 - 30%.